Heavy duty & off-highway Diesel Fuel Injection

Rich OE legacy
Our heritage dates back to the legendary CAV brand, and the introduction of in-line and the iconic DPA pump – the best-selling rotary pump worldwide. Both were revolutionary for their time, setting new standards for reliability and power, and we’ve continued to push the boundaries ever since.
Three choices for fleets
By providing three choices – new, reman and repair – we can provide fleet managers with convenient service and maintenance at a very competitive cost.
Latest generation OE technology
Our latest generation F3 system takes engines beyond the 2021 global emissions and fuel economy regulations and through the next decade. Based on our proven Euro VI Common Rail technology and capable of 3,000 bar injection pressure, it delivers a substantial improvement in emissions, fuel economy and refinement for the lifetime of the engine.
OE-approved repair
In addition to new and remanufactured units, we also offer authorised repair through our global network of Delphi Diesel Centres. Replacing all wearable and performance critical parts, with like-for-like OE, and using OE-approved test plans and equipment, it offers a quality but economical solution.
Find your local diesel specialist here.
Reman
For an equally fast, yet more cost-effective turnaround we offer a range of remanufactured parts. Available off-the-shelf, typically within one to two years of vehicle launch, they are built using OE parts, equipment and processes, and are calibrated to exacting OE specifications.


OE expertise in the aftermarket
Of course, we’re committed to supporting these technologies in the aftermarket. We offer a range of new OE components, identical to those originally fitted, including our pioneering Electronic Unit Injector, Electronic Unit Pump, Smart injector and Multec® Common Rail.
Commercial vehicle diagnostics and test
Our dedicated diagnostic solution for trucks, buses and trailers, supports the key commercial vehicle manufacturers and systems, including the ability to carry out dosing tests, Adblue freeze monitoring calibration, system drain down and regeneration of the SCR system. We also offer a range of OE-approved test equipment for quick and accurate test and repair of the latest heavy duty applications.
Training from the OE experts
Designed to help you prepare for the very latest heavy duty diesel fuel injection technologies, our extensive training programme covers the repair of key systems, including Electronic Unit Injector and Pump and Smart injectors. Learn more about our training.
.jpg?sfvrsn=950636e0_7)
The Delphi Difference
-
100 years of OE experience, supplier to the world’s top automakers
-
OE heritage and knowledge built into every aftermarket part
-
Comprehensive portfolio for a wide range of vehicles and model years
-
Streamlined SKUs for easy inventory management
-
Support through tools, tips and training

Related product resources and downloads
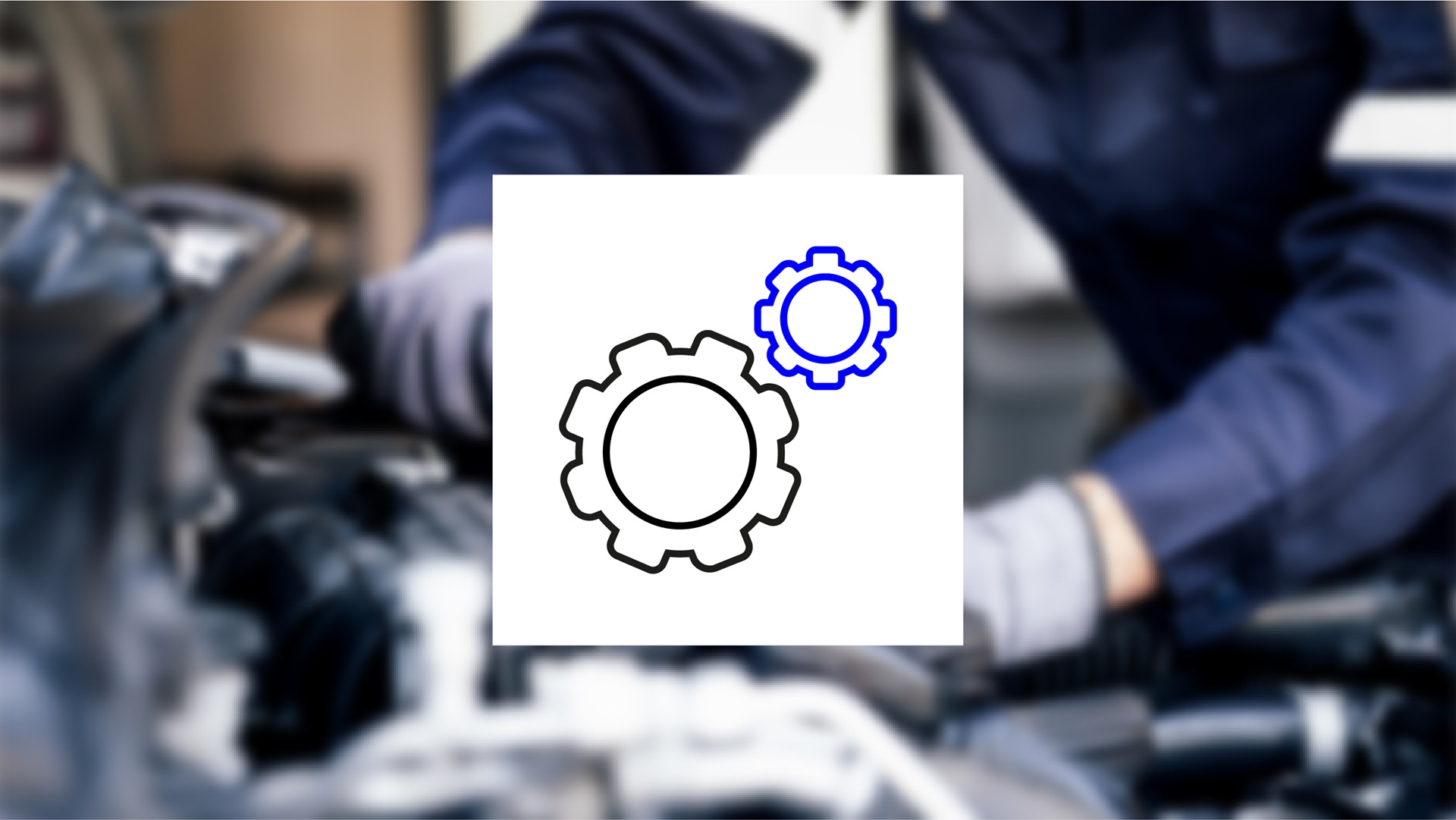
Resource Highlights
Unlike repair or reclamation, remanufacturing involves the comprehensive disassembly of the entire turbocharger unit. This is supplied to the factory as core – used turbochargers which are returned as a ‘part exchange’ upon purchasing a replacement unit (Delphi offers a surcharge on all remanufactured turbochargers. This means that the price you pay for a replacement unit is reduced by a predefined amount when you return the used turbo for remanufacturing).
The first stage in the remanufacturing process is the strip down of the turbo into its individual constituent parts. Delphi remanufactured turbochargers are engineered to exacting specifications, and are guaranteed to meet or exceed the standards set by the OEM. As part of this process, we discard certain components which we know are at risk of underperforming if reused, even if they are currently functioning correctly. These are sent for recycling, and brand new replacement components are used upon reassembly.
Components which may be reused undergo a thorough cleaning process, which involves chemicals and processes specifically developed to bring the component back to an as-new condition without damage.
The next step is to measure and inspect every single component to ensure that it still fulfills all of the parameters which we require. Any components which do not meet the strict standards we demand are removed from the system, and sent for recycling.
Those components inspected and certified as fit for re-use are then combined with the necessary brand-new parts (which have been engineered to ensure stringent OE standards of quality are met), and the assembly process can begin.
After fitment of the main shaft into its bearing housing, and the installation of the compressor wheel, each and every turbo undergoes a number of industry-standard tests to ensure that it will perform to our stringent requirements. One such step is the dynamic balancing of the shaft assembly. This ensures that each and every turbocharger will perform at its optimum, with minimum vibration, minimum bearing wear and minimum operating noise.
If the assembly is deemed to meet our standards, the final assembly of the compressor and turbine housings takes place, and additional pre-running checks are undertaken. This includes the setting and calibration of the turbochargers’ pressure-control system. Only after successful completion of each and every test is the remanufactured turbocharger ready to be signed off, packaged (along with an application-specific fitting kit and oil vessel) and sent for dispatch to another satisfied Delphi customer.
Get in touch

Find out where to buy Delphi parts
