Zintegrowany konwerter DC/DC i falownik
Zintegrowana konweter DC/DC i falownik (CIDD) firmy Delphi to rozwiązanie OE stworzone z myślą o hybrydowych pojazdach elektrycznych (HEV), hybrydach typu plug-in (PHEV) oraz pojazdach o napędzie elektrycznym (BEV) dostarczające maksymalną gęstość mocy w lżejszej, mniejszej i bardziej ekonomicznej formie.

Numer części OE | Zastosowanie | Numer części DT |
12368487431 | BMW 225XE (F45) , X1 (F49), M5 Sedan (F60) | PFV10000-12B1 |
Czym różni się falownik od konwertera DC/DC w pojeździe elektrycznym?
W pojazdach konwencjonalnych alternator ładuje akumulator, z którego pobierana jest energia do uruchomienia silnika spalinowego. W pojazdach hybrydowych i elektrycznych falowniki i konwertery zarządzają przepływem energii do akumulatora, a następnie do silnika i innych układów pokładowych.
Falownik zamienia prąd stały (DC) pobierany z akumulatora na prąd zmienny (AC) napędzając pojazd. Falownik steruje silnikiem i sprawia, że staje się on tymczasowym generatorem przekazującym energię hamowania z powrotem do akumulatora.
Konwerter steruje napięciem akumulatora, zwiększając je lub zmniejszając w zależności od układu i wymaganej mocy. Konweter DC/DC zazwyczaj obniża napięcie pochodzące z akumulatora do poziomu 12V potrzebnego do uruchomienia radia, reflektorów itp.
Części zamienne energoelektroniki zgodne z technologią OE
Dzięki wspólnej pracy falownika i przetwornicy możliwe jest zarządzanie napędem elektrycznym pojazdu oraz układami pomocniczymi. Dzisiejsze falowniki i konwertery mają z reguły skomplikowaną budowę, są drogie i ulegają awariom z powodu przegrzania. Są ciężkie, zajmują sporo miejsca w pojeździe, zmniejszając przestrzeń bagażową i pasażerską. Rozwiązanie OE od Delphi łączy falownik z konwerterem DC/DC w jeden zespół.
Zintegrowany konweter DC/DC i falownik (CIDD) od Delphi jest ekonomiczny, lekki i pozwala zaoszczędzić miejsce w pojazdach hybrydowych i elektrycznych (HEV), hybrydach typu plug-in (PHEV) oraz w pojazdach elektrycznych (EV). Korzystając z nowej opatentowanej technologii OEy - wyłącznika zasilania Viper pozwalającego na obustronne chłodzenie falownika - rozwiązaliśmy problem przegrzewającego się falownika, dostarczając wyższą moc wyjściową, przy jednoczesnym zachowaniu bardziej kompaktowej konstrukcji i zwiększonego zasięgu pojazdu.
Zintegrowany konweter & DC/DC i falownik (CIDD)

- Zwiększona trwałość i niezawodność dzięki rozwiązaniom zaprojektowanym z myślą o warunkach panujących zarówno pod maską, jak i na zewnątrz pojazdu, czyli czynnikach takich jak zanieczyszczenia i skrajnie wysokie temperatury.
- Poprawa funkcjonalności rozdzielnicy napięć, umożliwia uzyskanie zarówno niskiej, jak i wysokiej mocy wymaganej do zasilenia wszystkich elementów pojazdu od reflektorów po wspomaganie układu kierowniczego i klimatyzację.
- Pozwala na maksymalne wykorzystanie przestrzeni w pojeździe, dzięki przeniesieniu jednostki DC/DC z jej standardowej lokalizacji z tyłu pojazdu na przód pojazdu.
- Brak okablowania, przewodów chłodzących, połączeń i obudowy to większy zakres mocy i minimalizacja jej strat, przy jednoczesnym uproszczeniu obsługi i napraw pojazdu.
Aby dowiedzieć się więcej o częściach zamiennych jakości OE do pojazdów elektrycznych, skontaktuj się z przedstawicielem marki Delphi.
Zalety produktów Delphi
-
100 lat doświadczenia na OE, dostawca dla czołowych światowych producentów samochodów
-
Dziedzictwo OE i wiedza wbudowana w każdą część na rynku wtórnym
-
Kompleksowe portfolio dla szerokiej gamy pojazdów i lat modelowych
-
Usprawnione jednostki SKU dla łatwego zarządzania zapasami
-
Wsparcie poprzez narzędzia, wskazówki i szkolenia

Powiązane zasoby i pliki do pobrania dotyczące produktów
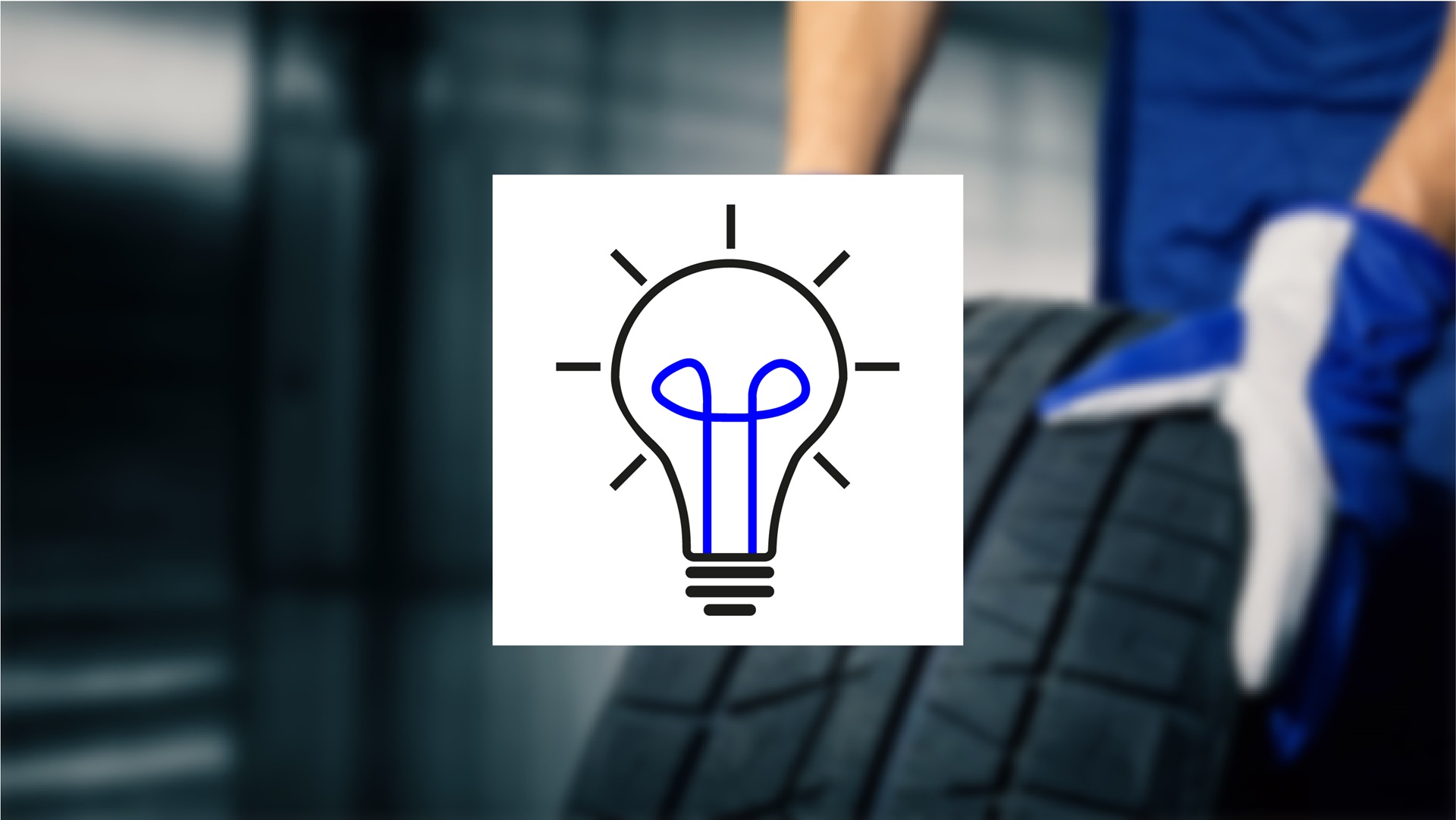
Najważniejsze informacje o zasobach
Proces regeneracji turbosprężarki wymaga dużej wiedzy technicznej oraz zaawansowanego sprzętu do przeprowadzenia testów i kalibracji. W przeciwieństwie do naprawy lub prostej regeneracji, regeneracja fabryczna wymaga kompleksowego demontażu całego zespołu turbosprężarki. Jest on dostarczany do fabryki w postaci rdzenia, czyli zużytej turbosprężarki zwracanej przy zakupie części zamiennej (Firma Delphi stosuje kaucje dla wszystkich regenerowanych turbosprężarek. Oznacza to, że cena jednostki zamiennej jest pomniejszana o określoną kwotę, o ile dokona się zwrotu zużytej turbosprężarki w celu przeprowadzenia jej regeneracji).
Regeneracja: na czym polega?
Proces regeneracji turbosprężarki wymaga dużej wiedzy technicznej oraz zaawansowanego sprzętu do przeprowadzenia testów i kalibracji.
W przeciwieństwie do naprawy lub prostej regeneracji, regeneracja fabryczna wymaga kompleksowego demontażu całego zespołu turbosprężarki. Jest on dostarczany do fabryki w postaci rdzenia, czyli zużytej turbosprężarki zwracanej przy zakupie części zamiennej (Firma Delphi stosuje kaucje dla wszystkich regenerowanych turbosprężarek. Oznacza to, że cena jednostki zamiennej jest pomniejszana o określoną kwotę, o ile dokona się zwrotu zużytej turbosprężarki w celu przeprowadzenia jej regeneracji).
Pierwszym etapem procesu regeneracji fabrycznej jest rozebranie turbosprężarki na poszczególne części składowe. Turbosprężarki regenerowane przez firmę Delphi są konstruowane zgodnie z rygorystycznymi specyfikacjami i gwarantują zgodność z normami wyznaczonymi przez producentów OEM, a nawet przewyższają ich wymagania. W ramach tego procesu odrzucamy elementy, wobec których istnieje ryzyko, iż ich ponowne wykorzystanie może powodować obniżenie parametrów pracy, nawet jeśli obecnie elementy działają prawidłowo. Są one przekazywane do utylizacji, a podczas montażu w ich miejsce stosowane są nowe części zamienne.
Elementy do ponownego ponownego wykorzystania poddawane są procesowi dokładnego czyszczenia z zastosowaniem precyzyjnie dobranych środków chemicznych i procedur, które zapewniają przywrócenie ich do stanu identycznego z nową częścią, nie powodując uszkodzeń.
Kolejnym krokiem jest pomiar i kontrola każdego z elementów, aby upewnić się, że nadal zapewniają wymagane parametry. Wszelkie elementy nie spełniające restrykcyjnych standardów są usuwane z układu i przekazywane do utylizacji.
Elementy sprawdzone i określone jako zdatne do ponownego wykorzystania są łączone z nowymi elementami (zaprojektowanymi zgodnie z restrykcyjnymi normami OE), następnie połączone części są gotowe do dalszego montażu.
Po zamocowaniu wału głównego w obudowie łożyska i zamontowaniu koła sprężarki, każda turbosprężarka przechodzi szereg testów branżowych, zapewniających zgodność z naszymi restrykcyjnymi wymaganiami. Jedną z procedur jest dynamiczne wyważanie zespołu wału. Dzięki tej czynności każda turbosprężarka zachowa optymalną wydajność przy minimalnym poziomie wibracji, zużycia łożyska i hałasu podczas pracy.
Jeśli zespół zostanie uznany za zgodny z naszymi standardami, następuje ostateczny montaż obudów sprężarki i turbiny oraz są wykonywane czynności kontrolne przed uruchomieniem. W ich skład wchodzi nastawa i kalibracja układu regulacji ciśnienia turbosprężarki. Dopiero po zakończeniu wszystkich testów zregenerowana turbosprężarka jest oznaczana jako gotowa, umieszczana w opakowaniu (wraz z odpowiednim do zastosowania zestawem montażowym i zbiornikiem oleju) i przekazywana do wysyłki do kolejnego usatysfakcjonowanego klienta Delphi.
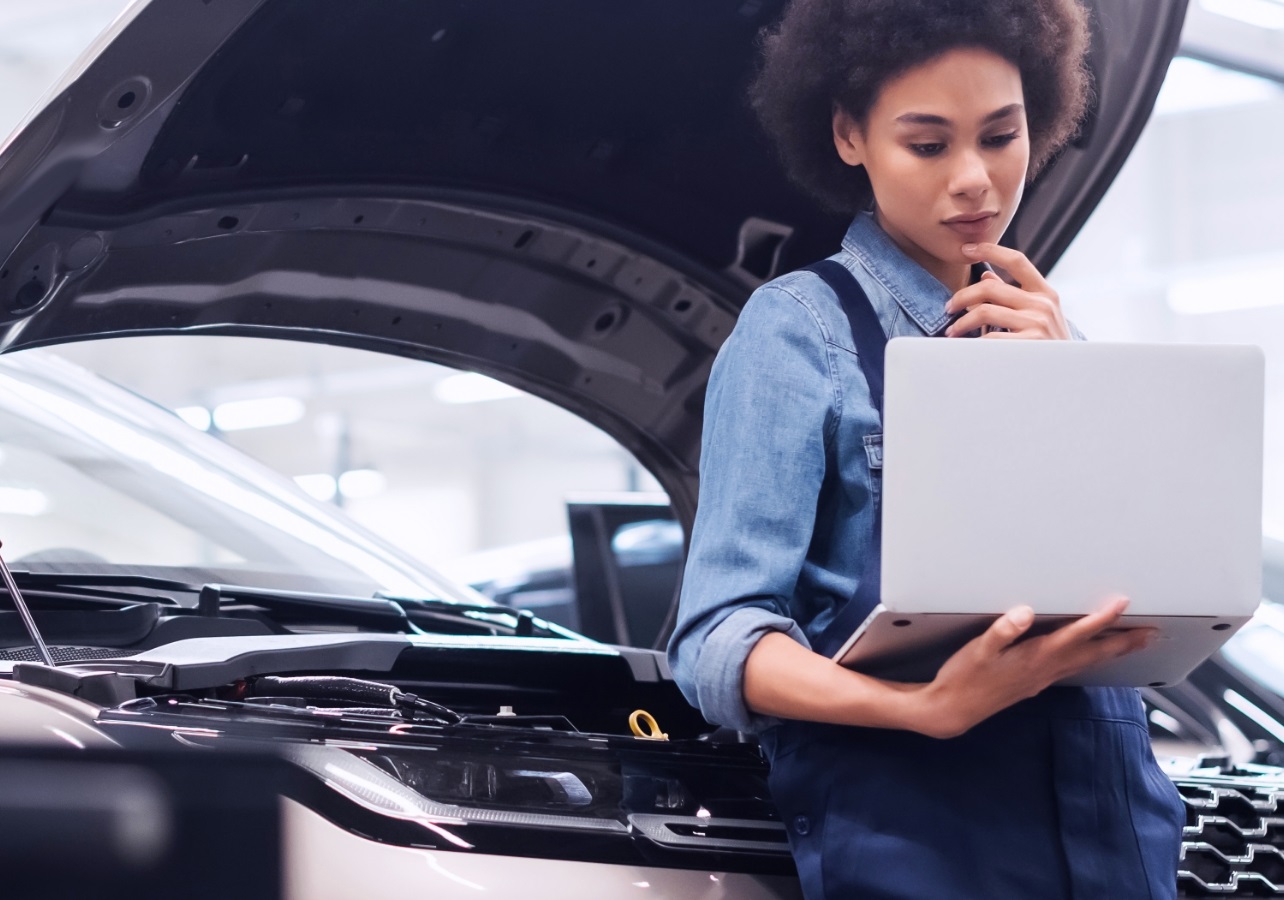
Visit our Technician Library for access to Documents and Downloads
Skontaktuj się z nami
Pełna gama produktów Delphi Energoelektronika
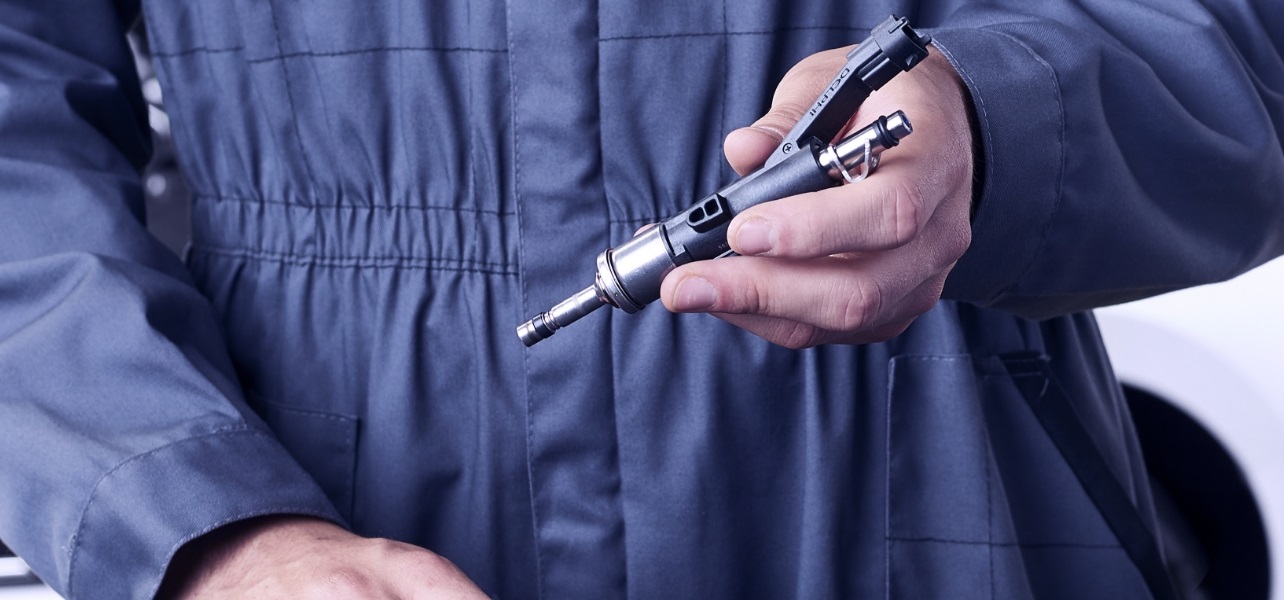
Dowiedz się, gdzie kupić części Delphi
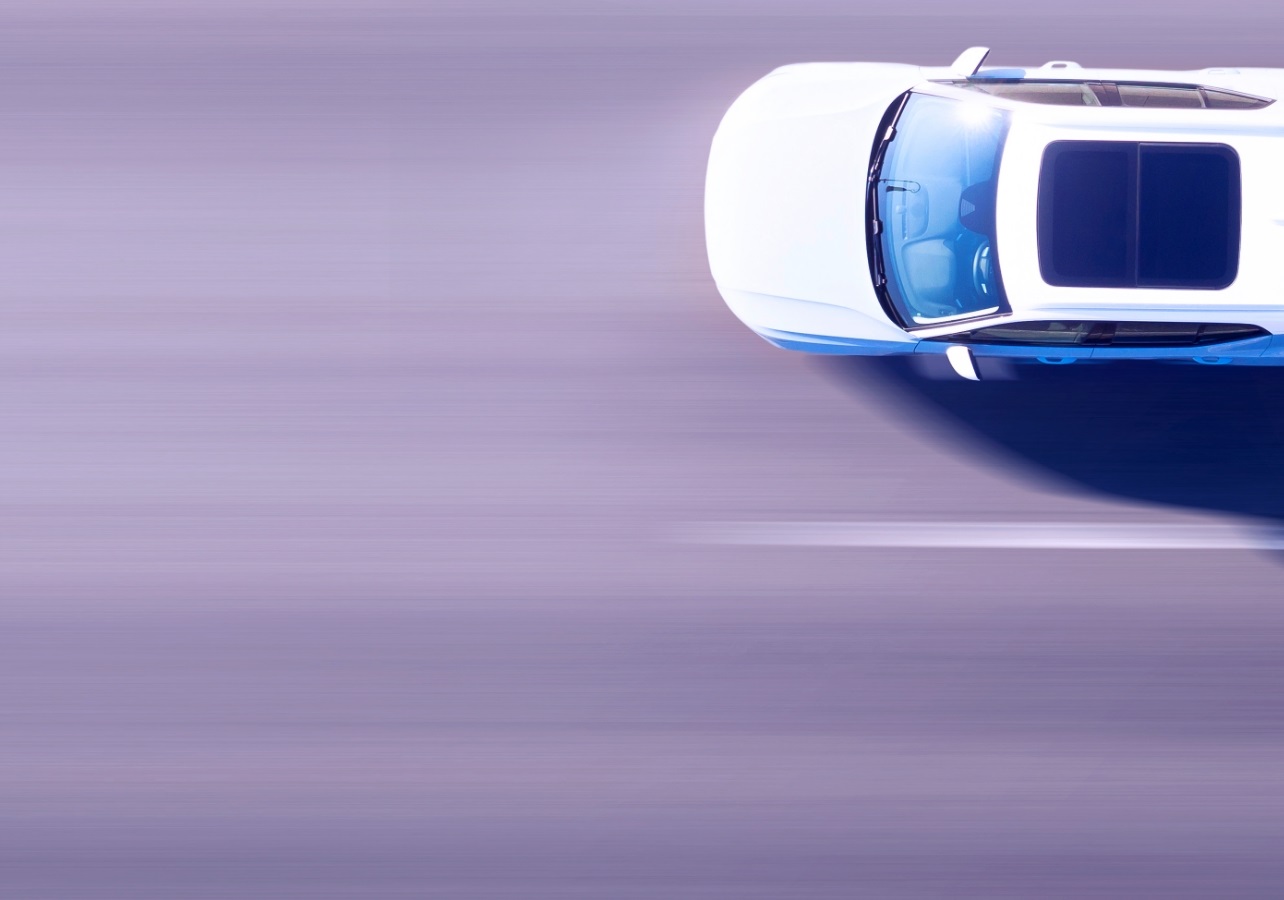