Brake Discs
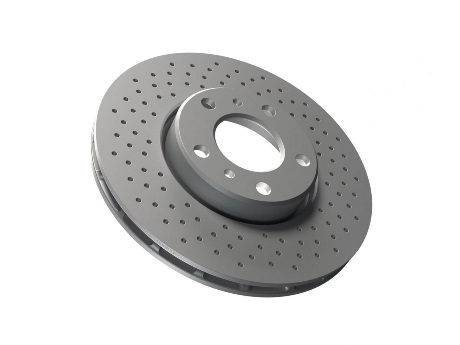
ECE R90 certified brake discs
It should come as no surprise that our brake discs for new vehicles launched post 1 st November 2016 are R90 certified, alongside a range for popular older applications. After all, we’ve been meeting these quality standards for many years. The only difference today: our discs now undergo official ECE R90 testing schedules including performance, dynamic friction comparison, high load integrity and thermal fatigue analysis to certify that they perform to a prescribed tolerance of the OE part.
Learn more about Delphi’s R90 certified brake discs and why it matters.

Fully coated brake discs
Thanks to a special zinc-flake, silver Geomet coating, our coated brake discs offer greater and longer-lasting corrosion protection compared with many oil-dipped or partially painted and coated equivalents, whilst also being more cosmetically appealing. And because they have no oil to clean off, they save valuable labour and service time. All this makes for a better protected disc that’s easier to install, easier to dismount as well as being easy on the eye too.

High-carbon brake discs
The added carbon content in our high-carbon discs helps to both reduce the risk of thermal cracking under high-temperature loads, and allows the discs to operate at a cooler temperature, for a more consistent braking performance. It also increases their resistance to distortion or warping for added durability, while delivering noise and judder free braking.
Cross-drilled brake discs
As well as looking cool from behind your wheels, our cross-drilled discs will keep your brakes feeling the same way – cool. The cross-drilled holes dissipate heat, brake dust and gases, helping to keep the pad surface cool and clean and reducing the risk of thermal distortion and warping. These same holes also prevent a film of water forming during wet conditions for improved braked response.

Vented brake discs
Our vented discs feature special internal cooling passages to maximise airflow. By continually moving air across the disc’s surface or through the disc itself, they allow more heat to be dissipated, improving both cooling capacity and resistance to cracking from thermal shock.
Brake discs with bearings
To avoid damage to the bearing during removal, and ensure the correct pressing in into the new, we offer a range of discs with these safety critical components already pre-mounted. They also include both toothed and magnetic ABS sensor rings, as per the OE, and the relevant fixing accessories. All for quick and accurate installation.
One-piece cast iron brake discs
Our one-piece cast iron discs offer an aftermarket alternative to BMW’s patented two-piece bi-metallic composite disc. Engineered from a single piece of cast iron, they deliver the same standards of consistency, longevity and braking performance as the two-piece disc, but at a fraction of the price. And to top it off, they come with fixing screws for quicker and easier fitting.
The Delphi Difference
-
100 years of OE experience, supplier to the world’s top automakers
-
OE heritage and knowledge built into every aftermarket part
-
Comprehensive portfolio for a wide range of vehicles and model years
-
Streamlined SKUs for easy inventory management
-
Support through tools, tips and training
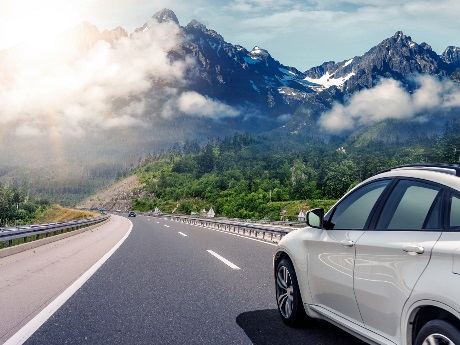
Related product resources and downloads
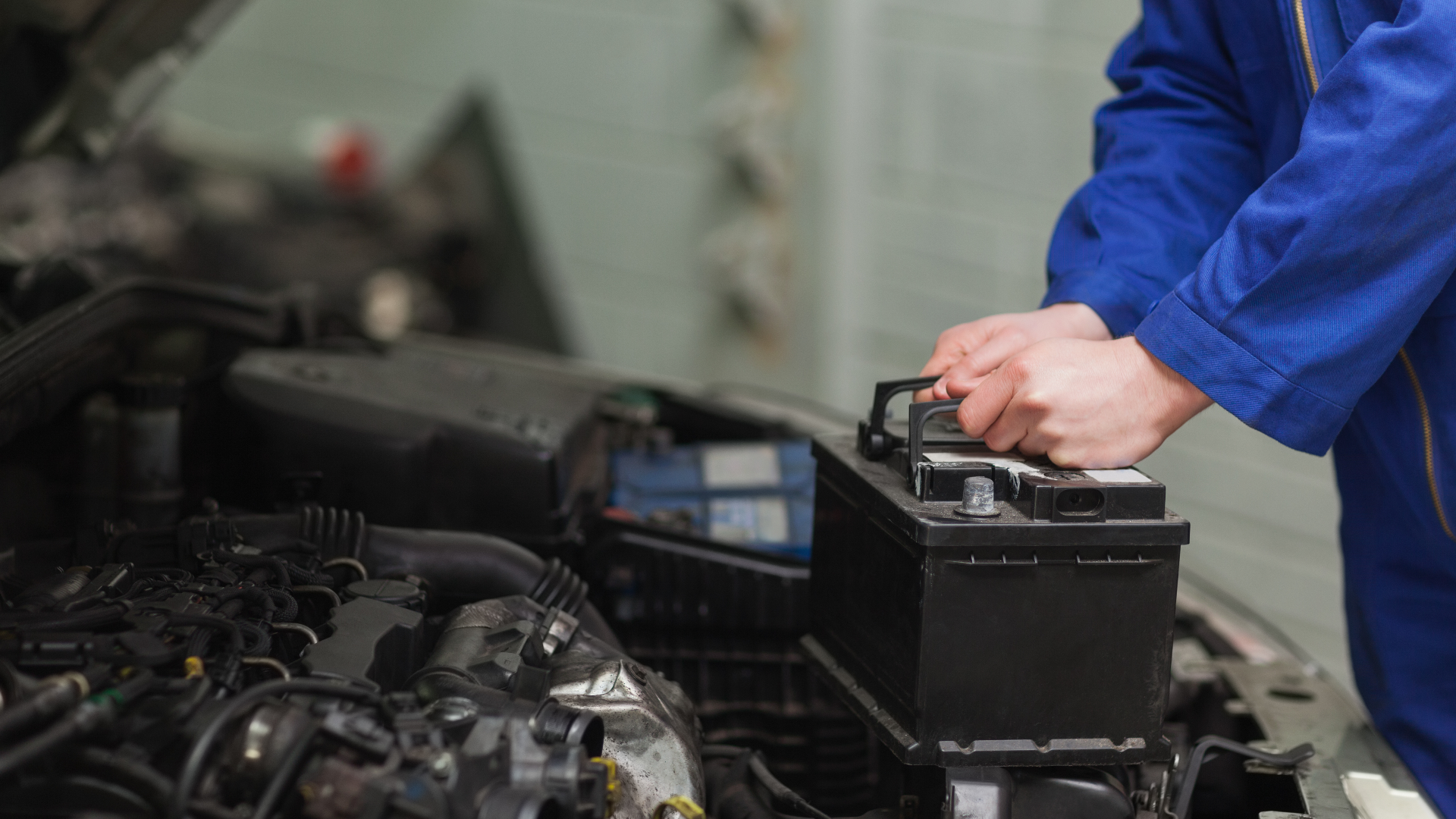
Resource Highlights
In this article you will find out about directional brake pads:
As automotive technology evolves, and with it customer expectations for a quieter more relaxing ride, manufacturers are turning to increasingly innovative materials and designs to reduce noise, vibration and harshness, or NVH for short. One of these being the use of directional brake pads.
These latest technology pads will also be a welcome addition in the aftermarket, since brake noise is one of the biggest causes of customer comebacks for many garages. Technicians, however, will need to be aware of the subtle differences in form, and more importantly fit, versus traditional pads, as fitting these noise reducing pads the wrong way, could actually have the opposite effect, creating unnecessary brake noise.
What is a directional brake pad?
When braking, standard pads are pressed evenly to the disc, and as a result can be pulled by the disc, causing vibration, and in turn, brake noise, reduced braking performance and uneven wear. In contrast, directional pads use either a chamfered friction surface or a crescent cut out of the shim and must be mounted in a specific direction, to ensure the pads are introduced to the disc at an angle. By creating the perfect angle for optimal pad to disc contact, they significantly reduce both noise and vibration.

A closer look at shims and chamfers
One of the most common causes of brake squeal is the movement between pads, caliper and discs. Brake shims are designed to help dampen this. Fixed on the rear of the pad - either mechanically attached, clipped and/or hot bonded - the finely tuned layers of dampening material help to reduce vibration, and therefore the transmission and amplitude of vibrational forces. They also add mass to the system, dampening vibrations in the pad and caliper, and act as a thermal insulator, ensuring uniform temperatures across the pad for more consistent braking and reduced heat transfer to the caliper and brake fluid. In a directional brake pad, the shim contains an additional crescent or half-moon cut out from the shim. This feature enables the piston to push the brake pad at a slight angle for both reduced noise and even pad wear.
Likewise, a chamfer is an angled cut or transitional edge between two surfaces of the pad. Engineered to compliment both the friction material and pad shape, it effectively controls how the edge of the pad interacts with the disc. Fitted to the leading
edge, and on some pads, the trailing edge too, chamfer directional pads prevent the leading edge of the brake pad from lifting and being pulled away from the disc. By ensuring optimal pad to disc contact, they help to reduce noise and uneven pad wear.
The right way to install a directional brake pad
Directional brake pads differ from standard pads in both their form, and of course their fit – they must be mounted in a specific direction, hence their name. Because of this, technicians should take time to inspect both the old and new pads for any visual signs as to their orientation. This may be as simple as following an arrow - many directional pads use either a letter, indicating which side of the vehicle the pad should be fitted to, R for the right-hand side and L the left, or an arrow showing the rotational direction of the disc and hence the direction in which the pad should be fitted.
However, if no arrow is present further measures need to be taken. For example, when installing chamfer directional pads, technicians should inspect the angular edge of the friction material. If only one chamfer is present the pad should be installed so the chamfer is the leading edge – in other words where the pad first contacts the brake disc. Alternatively, if there is a chamfer on both edges, the larger of the two should be installed as the leading edge.

Similarly, when installing crescent cut-out directional pads, the pad should be installed so the crescent or half-moon is again on the leading edge. Note it is important that the cut-out runs horizontally across the brake disc. This will help to ensure even pad wear and the correct distribution of force across the brake pad surface, reducing pad oscillation and preventing noise.

Fitting directional pads the wrong way may result in brake chatter and ultimately high pitch squeal. This will cost time and money to fix and worse still, could impact customer loyalty. As you can’t put a price on this, it pays to fit Delphi directional brake pads, and just as importantly, spending the time upfront to do it right!
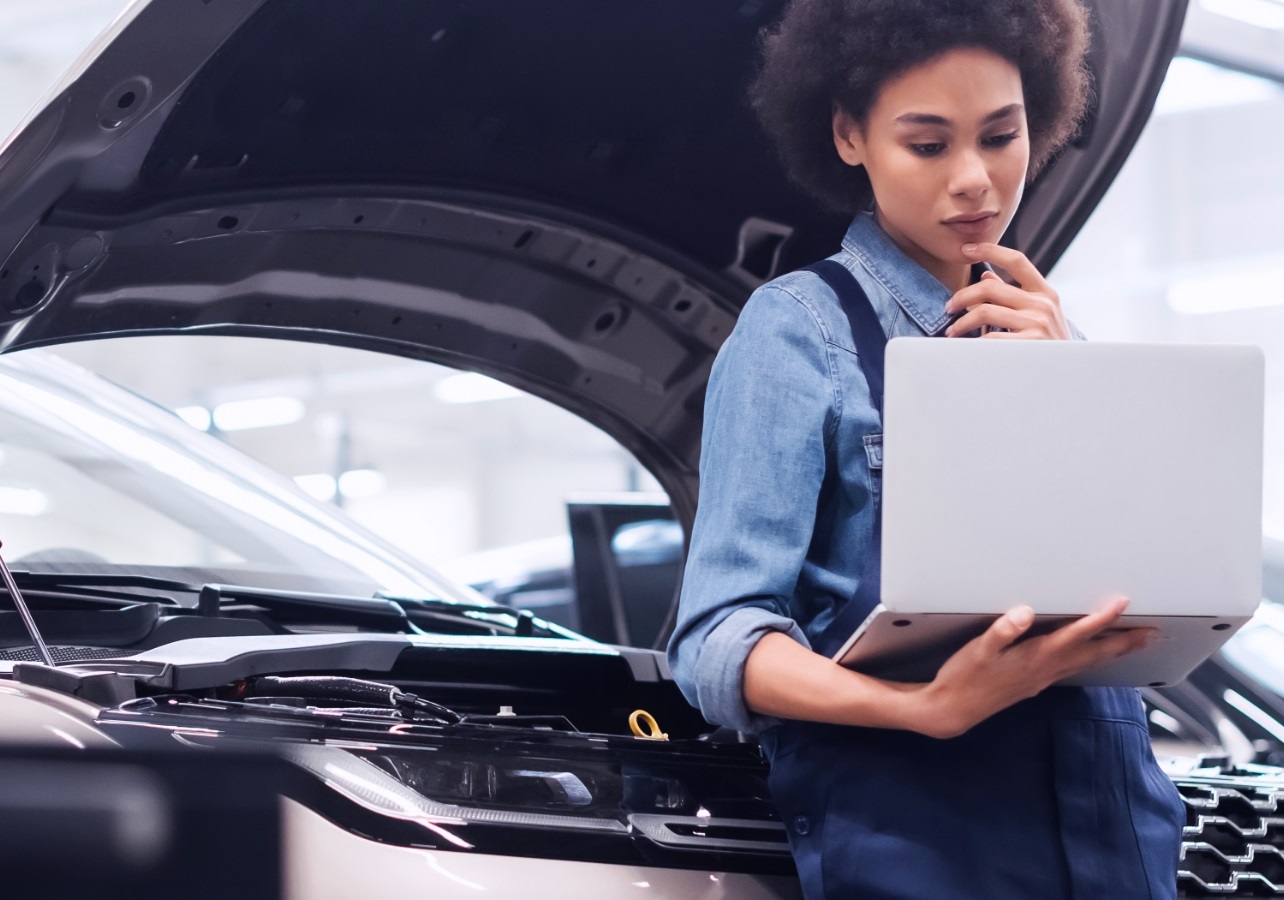
Visit our Technician Library for access to Documents and Downloads
Get in touch
The full Delphi product range
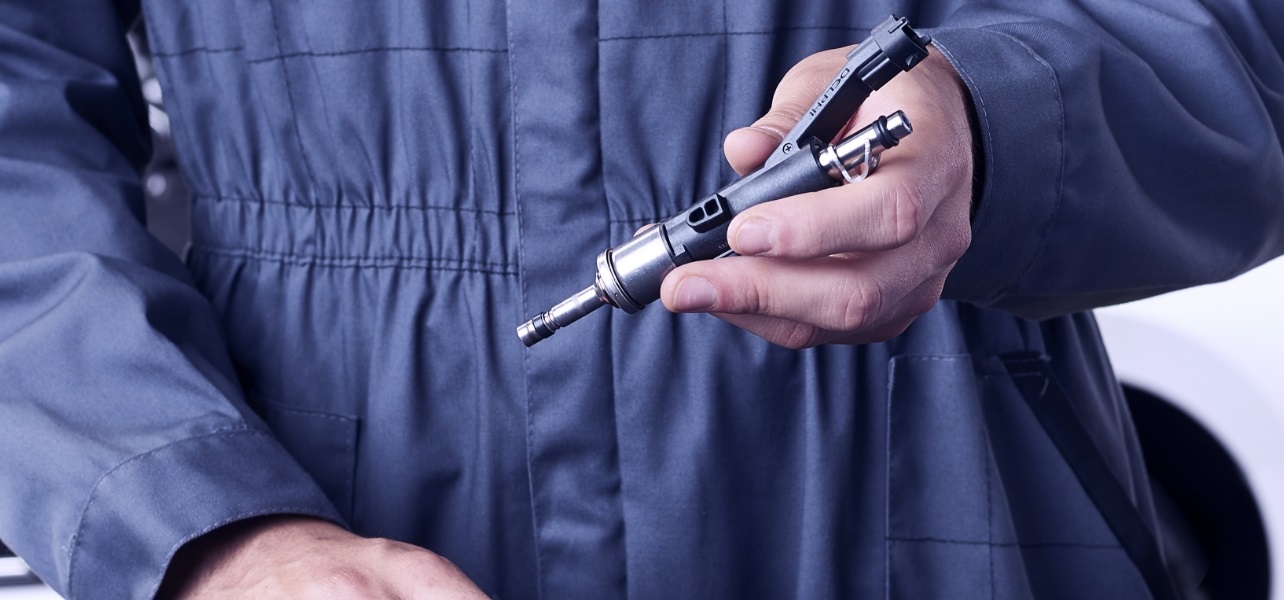
Find out where to buy Delphi parts
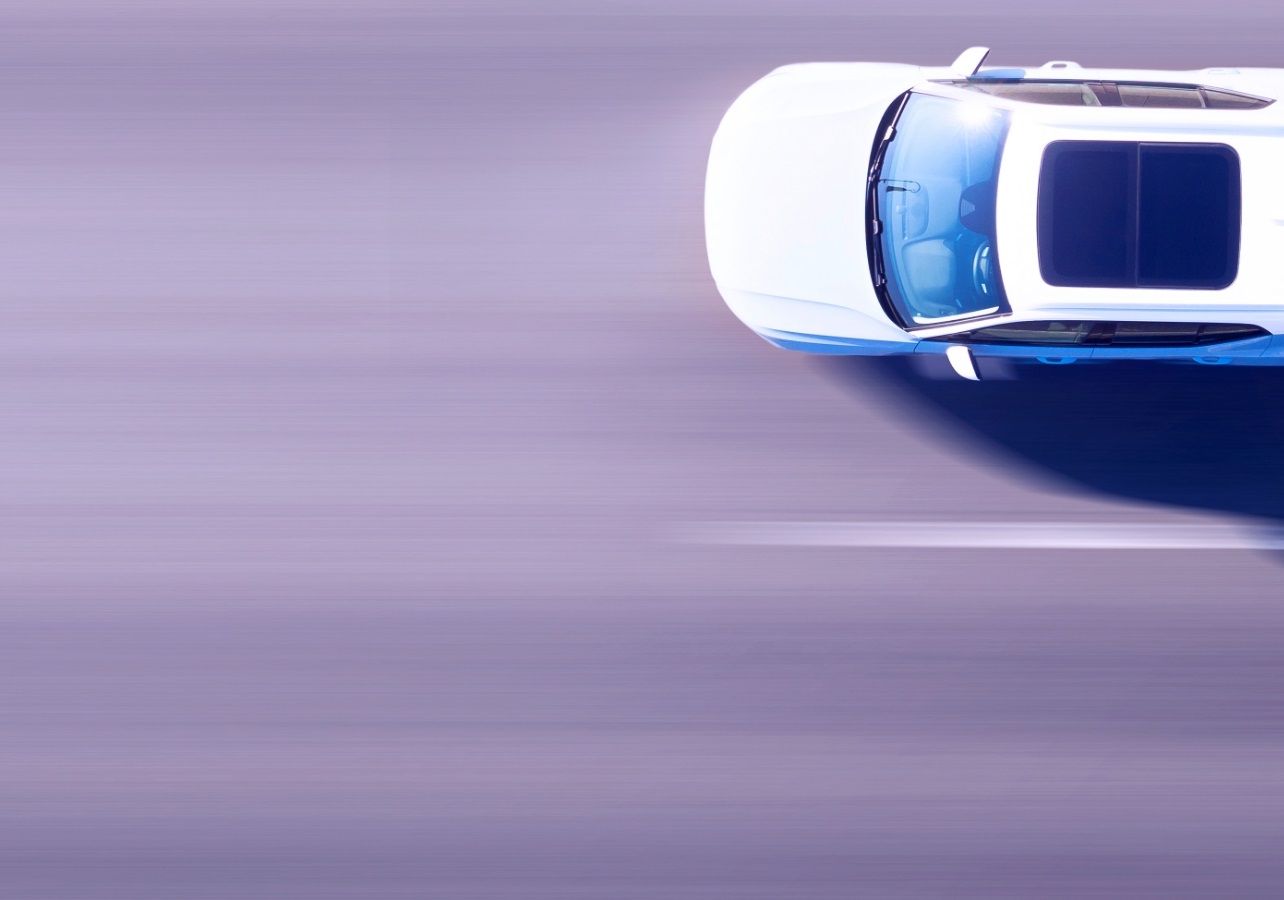