Brake Discs

ECE R90 certified brake discs
It should come as no surprise that our brake discs for new vehicles launched post 1 st November 2016 are R90 certified, alongside a range for popular older applications. After all, we’ve been meeting these quality standards for many years. The only difference today: our discs now undergo official ECE R90 testing schedules including performance, dynamic friction comparison, high load integrity and thermal fatigue analysis to certify that they perform to a prescribed tolerance of the OE part.
Learn more about Delphi’s R90 certified brake discs and why it matters.

Fully coated brake discs
Thanks to a special zinc-flake, silver Geomet coating, our coated brake discs offer greater and longer-lasting corrosion protection compared with many oil-dipped or partially painted and coated equivalents, whilst also being more cosmetically appealing. And because they have no oil to clean off, they save valuable labour and service time. All this makes for a better protected disc that’s easier to install, easier to dismount as well as being easy on the eye too.

High-carbon brake discs
The added carbon content in our high-carbon discs helps to both reduce the risk of thermal cracking under high-temperature loads, and allows the discs to operate at a cooler temperature, for a more consistent braking performance. It also increases their resistance to distortion or warping for added durability, while delivering noise and judder free braking.
Cross-drilled brake discs
As well as looking cool from behind your wheels, our cross-drilled discs will keep your brakes feeling the same way – cool. The cross-drilled holes dissipate heat, brake dust and gases, helping to keep the pad surface cool and clean and reducing the risk of thermal distortion and warping. These same holes also prevent a film of water forming during wet conditions for improved braked response.

Vented brake discs
Our vented discs feature special internal cooling passages to maximise airflow. By continually moving air across the disc’s surface or through the disc itself, they allow more heat to be dissipated, improving both cooling capacity and resistance to cracking from thermal shock.
Brake discs with bearings
To avoid damage to the bearing during removal, and ensure the correct pressing in into the new, we offer a range of discs with these safety critical components already pre-mounted. They also include both toothed and magnetic ABS sensor rings, as per the OE, and the relevant fixing accessories. All for quick and accurate installation.
One-piece cast iron brake discs
Our one-piece cast iron discs offer an aftermarket alternative to BMW’s patented two-piece bi-metallic composite disc. Engineered from a single piece of cast iron, they deliver the same standards of consistency, longevity and braking performance as the two-piece disc, but at a fraction of the price. And to top it off, they come with fixing screws for quicker and easier fitting.
The Delphi Difference
-
100 years of OE experience, supplier to the world’s top automakers
-
OE heritage and knowledge built into every aftermarket part
-
Comprehensive portfolio for a wide range of vehicles and model years
-
Streamlined SKUs for easy inventory management
-
Support through tools, tips and training

Related product resources and downloads
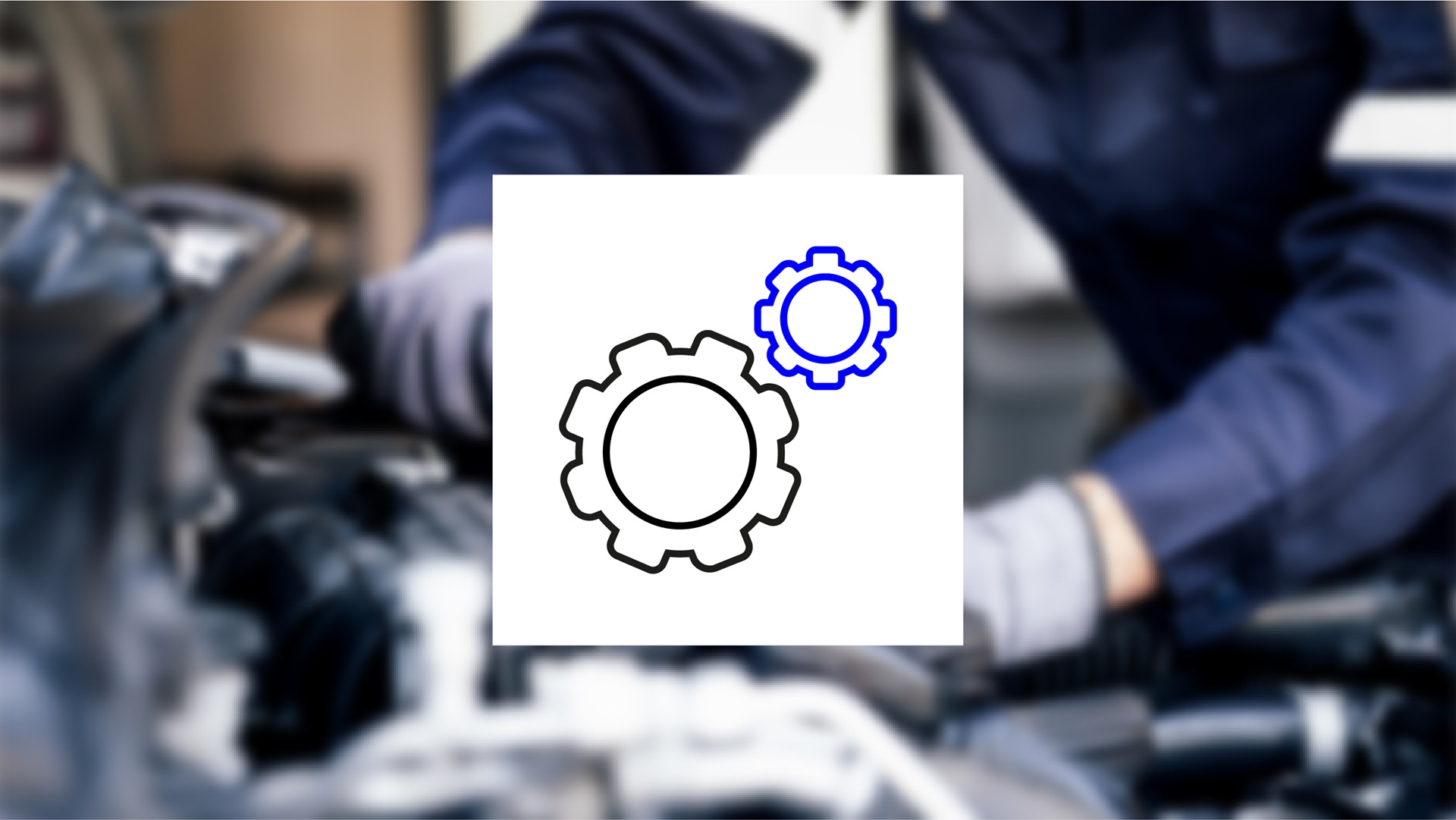
Resource Highlights
In this article, you will find out about brake pad sensors, including what they are, how they work and when they need to be replaced.
Now fitted as standard on many modern vehicles, brake pad wear sensors, also known as brake pad wear indicators, will become an increasingly popular part of any brake job. So, it’s essential you know both how they work. And when to replace them….
What is a brake pad wear sensor?
Brake pads wear over time. However, the amount of time it takes to do this can vary greatly. Road conditions, driving style, speed, load, and the type of pads and discs can all impact the speed at which this happens, making it difficult for drivers, and technicians, to determine when a new set may be needed. The introduction of the brake pad wear sensor removes this uncertainty by letting drivers know when the pad has worn, and in some cars, even predicting when this will be. As well as helping plan future brake jobs, it also ensures the brake pads are in good working order for a safe and controlled ride.

How do brake pad wear sensors work?
Today’s brake pad sensors are an evolution of the traditional metal tabs found in many older braking systems. By rubbing against the discs, these make a loud screeching sound, providing an audio clue to the driver that the pads have reached their maximum wear limits.
Electronic brake pad wear sensors eliminate the tab by using a small sensor - a loop of wire with a low current passing through it. As the pad wears out, the loop is exposed and make contacts with the rotor or disc, creating an open circuit. This illuminates the dashboard warning light, indicating it’s time to replace the brake pads.
The latest sensors go one step further. As well as alerting the driver to a worn pad, they can also gauge how much mileage is left. Known as two-stage sensors, they feature two resistor circuits that run parallel with each other at different heights in the sensor housing. When the first circuit is breached, resistance in the sensor increases and the system calculates how much life is left in the brake pad using inputs such as wheel speed, mileage, brake pressure, brake temperature and brake operating time. This information is displayed on the dashboard, either as a physical number on vehicle start up, or a warning light which changes colour as the pad wears. Once the second circuit is broken, the circuit becomes open. This triggers the warning light that advises it’s time for a brake service.
Whilst many brake pad wear systems feature a sensor on the inboard pad at each corner of the vehicle, the number can vary - between one and four – depending on the design of the braking system. The position of the senor can also vary. The most common type of electronic wear sensors are embedded directly in the brake pad material, and therefore are not removable. Others are mounted on the brake pad itself.
When do brake pad wear sensors need to be replaced?
As brake pad wear sensors are designed to break, they should be replaced as a matter of course every time new brake pads are fitted. It’s also advisable to regularly inspect the sensors, in between pad changes, and replace where necessary. Over time, heat from the brakes can damage both the wiring and clips. They are also prone to damage during other work on the vehicle such as installing new brake discs.
To meet the growing demand for replacement parts, Delphi provides a wide range of OE quality brake pad wear sensors, available either with the pads, as per the OE, or as individual items.

Visit our Technician Library for access to Documents and Downloads
Get in touch
The full Delphi product range

Find out where to buy Delphi parts
